
Artificial intelligence optimises paper production processes
Fluctuating values on the machines can lead to rejected products and expensive downtime in paper production. An intelligent software solution analyses the data so that the relevant parameters can be adapted and the risks minimised.
Challenge: identifying fluctuations earlier
In industrial paper production, the values for grammage and moisture of produced tracks vary on the paper machine. Smaller fluctuations within specified tolerances are not a problem for the ongoing production process or the final product quality. But significant deviations from the target have serious consequences: if grammage is too low, for example, the paper can only be sold at a much reduced price as a special item – or it may even end up as a worthless reject. But that’s not all: drastic fluctuations in grammage and moisture can also cause paper on the produced track to tear, which leads to costly downtime of the paper machine and an insurance-related business interruption. At the moment such fluctuations are usually detected too late and adjustments to correct them in time are no longer possible by that point.
‘With a manageable investment of time and resources and based on existing data, a sustainable increase in different values is achieved in paper production.’
Solution: controlling material density using AI
This is where the company Craftworks comes in as a partner in the Funk Beyond Insurance network. ‘Fluctuations in grammage and moisture can be attributed to deviations of another value: the material density,’ explains Manuel Zimmermann, Beyond Insurance Manager at Funk. In the upstream production process, the material density can be influenced in a targeted way through a number of control parameters, such as the amount of thick matter, to avoid losses in quality later down the line. Craftworks uses individual solutions here that focus on artificial intelligence (AI): in the case of this Funk client, the process and machine data already extensively recorded on the industrial paper machines is used to teach an AI application. Based on patterns within the control parameters and statistical correlations of the target parameters of grammage and moisture, AI is able to provide recommendations for the optimal configuration of control parameters on the paper machine.
Artificial intelligence (AI)
KI ist ein Überbegriff für softwarebasierte Anwendungen, die Intelligenzleistungen des menschlichen Gehirns replizieren – Lernen, Urteilen und das Lösen von Problemen. Sie basieren dabei im Wesentlichen auf Algorithmen zur Berechnung von Wahrscheinlichkeiten und dem Erkennen von Mustern in umfangreichen Datensets. Das wichtigste Merkmal von KI-Methoden ist die Lernfähigkeit, durch die sie nicht bloß auf Basis vorgegebener, auswendig gelernter Beispiele entscheiden, sondern in der Praxis gewonnenes Wissen verallgemeinern und neu anwenden können. Dadurch liefern KI-Anwendungen mit der Zeit immer bessere Ergebnisse zu der ihnen zugewiesenen Aufgabenstellung.
The end result is a software application that acts as a master controller for the paper machine: It receives the data from the production process via a defined interface. The application processes the data and then delivers a recommendation for controlling the material density as well as for influencing the grammage and moisture. Craftworks provides initial training at handover to ensure that all employees working in paper production are able to use the software. The application is then set up together in an IT infrastructure.
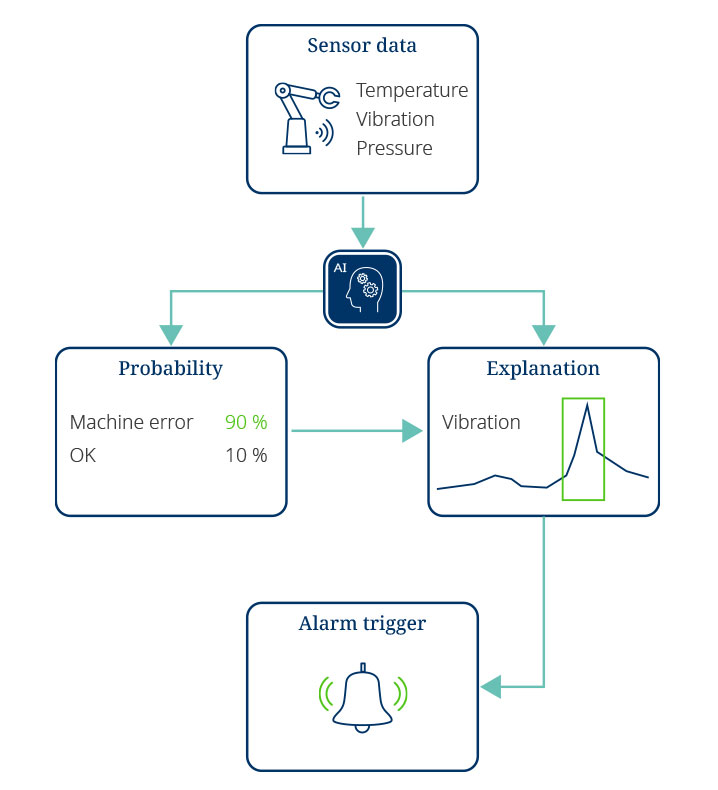
Benefit: reduced costs, high quality and efficiency
The optimised control of material density dramatically reduces fluctuations of grammage and moisture in the paper machine. This not only improves the quality of the produced paper and therefore the quality-related key performance indicators, but also increases the efficiency of production as it reduces downtime. Furthermore, the prevention of paper tears significantly reduces the risk of fire: torn tracks often run into the shafts underneath the paper machine, where they easily ignite. ‘With a manageable investment of time and resources and based on existing data, a sustainable increase in different values is achieved in paper production,’ says Dr Alexander Skorna, Head of Business Development at Funk. ‘Alongside production efficiency and product quality, this also includes process stability and general safety.’
Project progress: development without risk
Funk Beyond Insurance divides this type of project into multiple phases, in order to assess the approach early and be in a position to cancel the project directly if there are negative outcomes:
1. Kick-off workshop
Definition of application case and objectives as well as first analysis of the datasets
2. Data analytics phase
Definition of initial correlations and application cases
3. Development phase
Development of the model
4. Validation phase
Check and finalisation of the model
Manuel Zimmermann: ‘In each phase we assess whether the next phase will be feasible. This assessment is conveyed to the client so that the project risk is greatly reduced.’
Suitable for: industrial companies in a wide range of branches
Not just paper manufacturers, but also other industrial companies in a wide range of other branches can benefit from the technologies offered by Funk Beyond Insurance partner Craftworks. With its software solutions for predictive quality and predictive maintenance, the Vienna-based company specialises in the analysis of existing data from processes, machines and systems.
Predictive maintenance
Predictive Maintenance bzw. vorausschauende Wartung/Instandhaltung beschreibt das folgende Konzept: Ungeplante Maschinenstillstände, etwa durch Verschleiß oder Störungen, werden in geplante und bedarfsgerechte Instandhaltungsmaßnahmen überführt. Geeignete Sensorik erfasst dabei Parameter, die bei Abweichungen Rückschlüsse auf Verschleißerscheinungen oder beginnende Störungen zulassen – zum Beispiel die Temperatur eines Werkzeugs, Vibrationen einer Baugruppe oder die Anlaufzeit eines Motors. Charakteristische Muster in diesen Daten lassen sich durch geeignete Modelle mit konkret zu erwartenden Schäden verknüpfen.
Based on machine learning and deep learning technology, AI is able to predict errors and show which parameters are affecting product quality. As a result risks such as downtime or high rate of rejection are minimised, while costs are reduced and efficiency increased.
Your point of contact
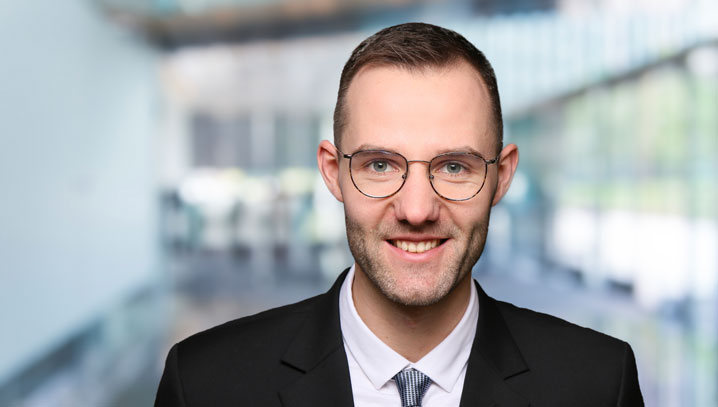
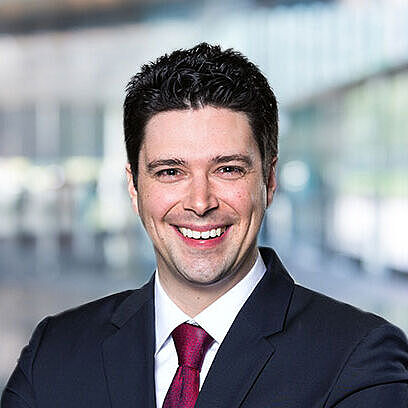
Technical aspects
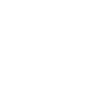
Machine/operating data
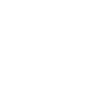
Artificial intelligence
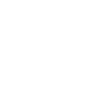
Software controller
Benefits/objectives
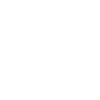
Risk reduction
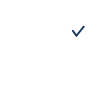
Product and process quality