
How sensor screws detect loads on machines
When technical production systems fail, this regularly leads to major financial damage. Sensor data and software analyses show whether load limits are being observed – and help technical personnel optimise their machines.
Challenge: avoid machine failure
When it comes to presses, rollers, machining centres and other machinery, damage often has serious financial consequences for businesses. Cost drivers in such an instance include not just direct material and personnel costs for replacement parts or repairs, but also operational delays due to reduced production capacities. Downtime for bottleneck systems even threatens full-blown business interruptions in the worst-case scenario. In addition, high claim ratios can then lead to increasing premiums for the associated insurance policies. ‘Often, machine damage is incurred by a business which the systems are not designed to handle, like constant excessive peak loads, extreme load changes or off-centre loads,’ explains Manuel Zimmermann, Beyond Insurance Manager at Funk.
Smooth process management or improved tool designs can somewhat reduce mechanical loads – but this approach can often not be implemented in practice. The reason: there is frequently no or not enough precise information on the real loads on the machine. Moreover, data analysis in many practical applications is so complicated that there is no analysis capability in the day-to-day running of the business.
Solution: detect loads with sensors
Funk Beyond Insurance partner ConSenses has collaborated with different machine manufacturers, press operators and tool engineers to develop a suitable range of sensors. The patented sensor screws can be used to quickly and precisely detect mechanical loads on production systems, such as presses, forging hammers or rolling mills. These sensors look like conventional machine screws with a plug-in connection in the head and meet established screw standards in terms of their design and load-bearing capability. As conventional as they seem on the outside, however, on the inside they have special sensors integrated, which are constantly detecting data. The data is analysed efficiently using in-house developed evaluation devices and control components.
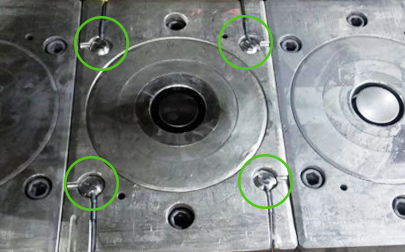
The ConSenses sensor screws are available in different designs that meet established ISO standards – in this example, they are installed in a tool along with signal cables. © Consenses
‘Since the sensor screws act as a connecting element, force signals can be read much more accurately than in, say, a solution using frame sensors,’ explains Dr Alexander Skorna, Head of Business Development at Funk. When the screw sensors are used in combination with special acceleration or reference sensors, relevant load parameters can be detected directly on the machine or even on or in the tool itself. Already existing information from controllers and IT systems is read in as needed via individual interfaces and the measured values from the sensor screws are automatically assigned. As a result, the course of loads for the individual working steps of the machine can be intelligently and precisely analysed over time.
Benefit: risk management meets process optimisation
Using the ConSenses solution, peak loads on technical production systems can be identified and reduced in a targeted way. This approach reduces the likelihood of machine damage, as load-intensive processes or parameters can be adjusted in due course. There are different financial and insurance-related benefits to this: for one, the high costs of system damage can be avoided through comparably cost-effective maintenance that anticipates problems before they occur, an approach known as predictive maintenance.
Predictive Maintenance
Predictive maintenance describes the following concept: unplanned downtime caused by wear and tear or faults is reallocated to planned, needs-based maintenance measures. Suitable sensors detect parameters that can be used to draw conclusions about wear and tear or potential faults – for example, a sensor might track the temperature of a tool, vibrations of an assembly or the start-up time of a motor. Characteristic patterns in this data can be linked to specifically expected damage through suitable models.
On the other hand, this approach produces direct touchpoints with Technical Property insurance, as the likelihood of cost-intensive major claims can be reduced. The recorded data can also be used perspectively as a basis for innovative parametric insurance solutions.
Parametric insurance
In the case of parametric insurance, the insurer adjusts claims based on predefined parameters rather than later damage amounts. If a contractually agreed value range is breached as a result of an event, this ‘trigger’ automatically results in an assigned claims payment in response. Any potential deviation of the claims payment from the actual amount of damage incurred remains as the ‘basic risk’. The increasing use of modern sensors and highly developed analysis software has facilitated the constantly improved recording of damage-relevant data flows on the one hand and the development of more reliable models for correlating trigger events and damage amounts on the other.
The installed sensors from Beyond Insurance partner ConSenses can even play a special role in the context of business interruption or loss of earnings insurance. After all, from a business and operational perspective, preventing business interruptions arising from machine downtime is often even more crucial than the damage to the property itself.
‘Datasets from installed sensors give machine manufacturers direct insight into the practical use of their products. This allows systems to be optimised directly.’
In addition to the scenario of just pure damage prevention, the technology also offers the potential to optimise processes, while simultaneously providing benefits to manufacturers of technical production systems such as presses or rolling mills. Currently manufacturers employ a mix of experience, calculations, assumptions and simulations to design their products and sell them to customers, without receiving any feedback after the fact besides the information received in the usual course of the aftersales processes. As Manuel Zimmermann says, ‘Datasets from installed ConSenses sensors give machine manufacturers direct insight into the practical use of their products. This can be used as a basis for optimising the systems and even be incorporated in the design of the systems with a view to how they will operate later.’ Machine manufacturers are increasingly adding operator models (‘pay-per-use’ or ‘as-a-service’ models) to their range of services. The load data from the sensor screws can be used to integrate availability guarantees for such business models with calculable residual risk into guarantee insurance policies.
Project progress: analysis based on individual need
The ConSenses technology is used in different setups:
- as a system on loan for screening critical systems or tools in the course of a project
- as an ‘edge device’ – a transmitter for data packets – when digitising existing and new systems
- as a protective against overloads in miniaturised systems
The typical course of a project is strongly based on the planned scope. ConSenses usually works in one of three types of project, which always involve an initial meeting, support during running operation and follow-up.
1. One-day measurement
A typical question here would be, for example, why do screws keep breaking in a forging tool? With a specific problem like this, ConSenses sets the objective in advance within a few days. After continuing exchange of information about the mechanical structure, the data to be recorded and the expected measured values, the necessary hardware is defined and integrated on site at the client’s premises within 20 minutes.
2. Measurement campaign alongside production
Problems such as unexpected cracks in machines take longer, as the systems are analysed during normal operation. In this case, for example, suitable hardware in the form of adapters is loaned to the customer for several weeks. ConSenses can then help conduct the measurements remotely via WiFi or UMTS and deliver regular status reports.
3. Small to large IoT installation
Where permanent monitoring and analysis are desired, ConSenses and the Funk Beyond Insurance team work together with their clients to implement entire IoT installations.
IoT
The 'Internet of Things', or IoT for short, is the common worldwide name for the concept of using modern communication technologies to create a consistently networked infrastructure. It is consisting of all physical and virtual elements of daily life: cars, smartphones, household appliances and online platforms. The industrial character of IoT is concretized in the ‘Industrial Internet of Things’ (IIoT) and is distinguished from the more end-consumer-oriented approach of IoT. The focus here is on the holistic networking of production plants, sensor technology, IT systems, workpieces and products within factories and entire supply chains.
For example, a standard package for monitoring pressing force was developed, comprising the following components:
- Con-rod sensors
- Solution for moved cables
- Charging amplifier with peak value memory
- Accelerometer
In larger IoT installations, the values are not just processed in the machine controls; an additional system for data processing is implemented on the machine. This system transmits the data to corresponding software for analysis. This way, a connection to the client’s existing IT infrastructure can be realised.
Suitable for: businesses with industrial production systems
ConSenses delivers quality data from technical systems for all industries. The aim of measurement technology is to create a balanced industrial production system. ConSenses has extensive experience and particular expertise in the area of presses and rollers and can offer systems for these directly. This expertise can also be transferred to other systems, however, such as flat rollers, rotary swaging, milling or turning. The Funk Beyond Insurance team is happy to help answer your initial queries.
More information about the ConSenses measurement system can be found in this video:
Your point of contact
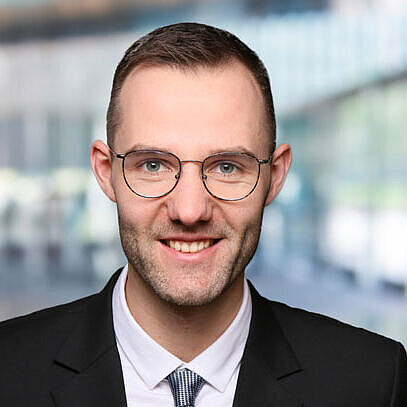
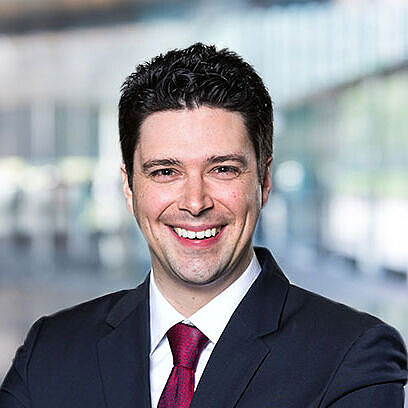
Technical aspects
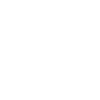
Sensor screws
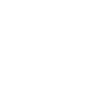
Machine/operating data
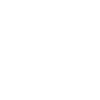
Intelligent data analysis
Benefits/objectives
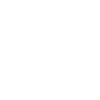
Risk reduction
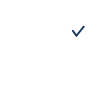
Product & process quality
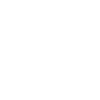
Predictive maintenance